Lavorazione degli ingranaggi
Capacità di lavorazione degli ingranaggi - weforging Manufacturing
Noi di Weforging Manufacturing siamo specializzati nella lavorazione di ingranaggi personalizzati per applicazioni industriali. Le nostre capacità spaziano dallo stampaggio a caldo e ad anello di ingranaggi grezzi alla lavorazione CNC di precisione, alla dentatura, alla sagomatura, alla rettifica e ai trattamenti superficiali. Forniamo agli OEM di tutta Europa e del Nord America soluzioni complete per ingranaggi, personalizzate in base a standard precisi.
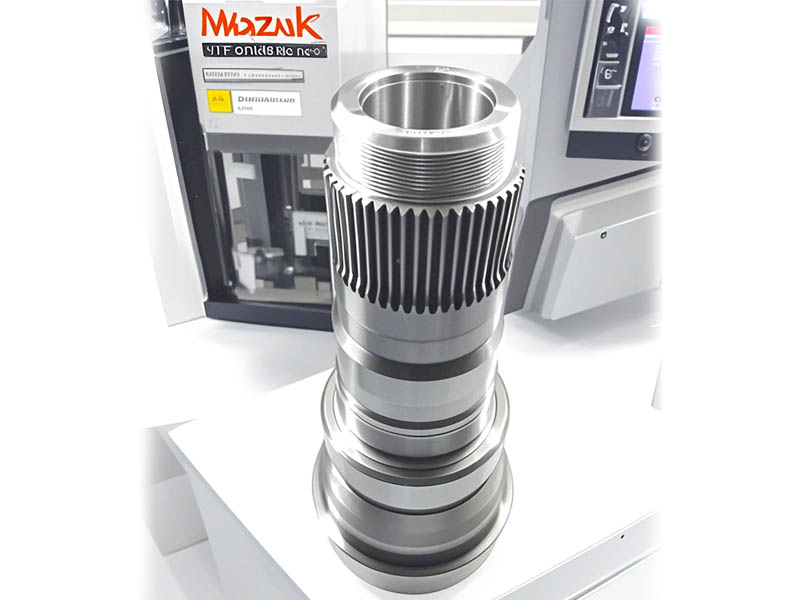
Che cos'è la lavorazione degli ingranaggi?
La lavorazione degli ingranaggi si riferisce a un insieme di processi che trasformano gli sbozzi di ingranaggi forgiati o fusi in ingranaggi finiti con profili di denti precisi. In genere comprende tornitura, dentatura, sagomatura, brocciatura, rettifica e trattamento termico. Offriamo soluzioni integrate a partire dalla forgiatura fino all’ispezione finale.
Tipi di ingranaggi che produciamo
- Ingranaggi cilindrici
- Ingranaggi elicoidali
- Ingranaggi conici
- Ruote dentate
- Scanalature interne ed esterne
- Profili di ingranaggi personalizzati su disegno del cliente
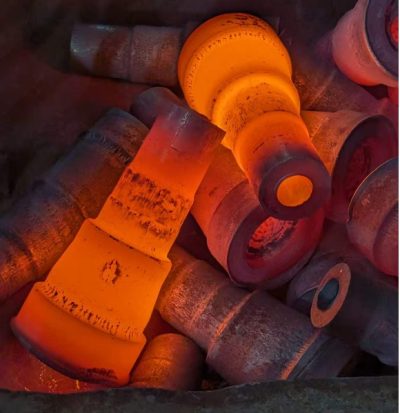
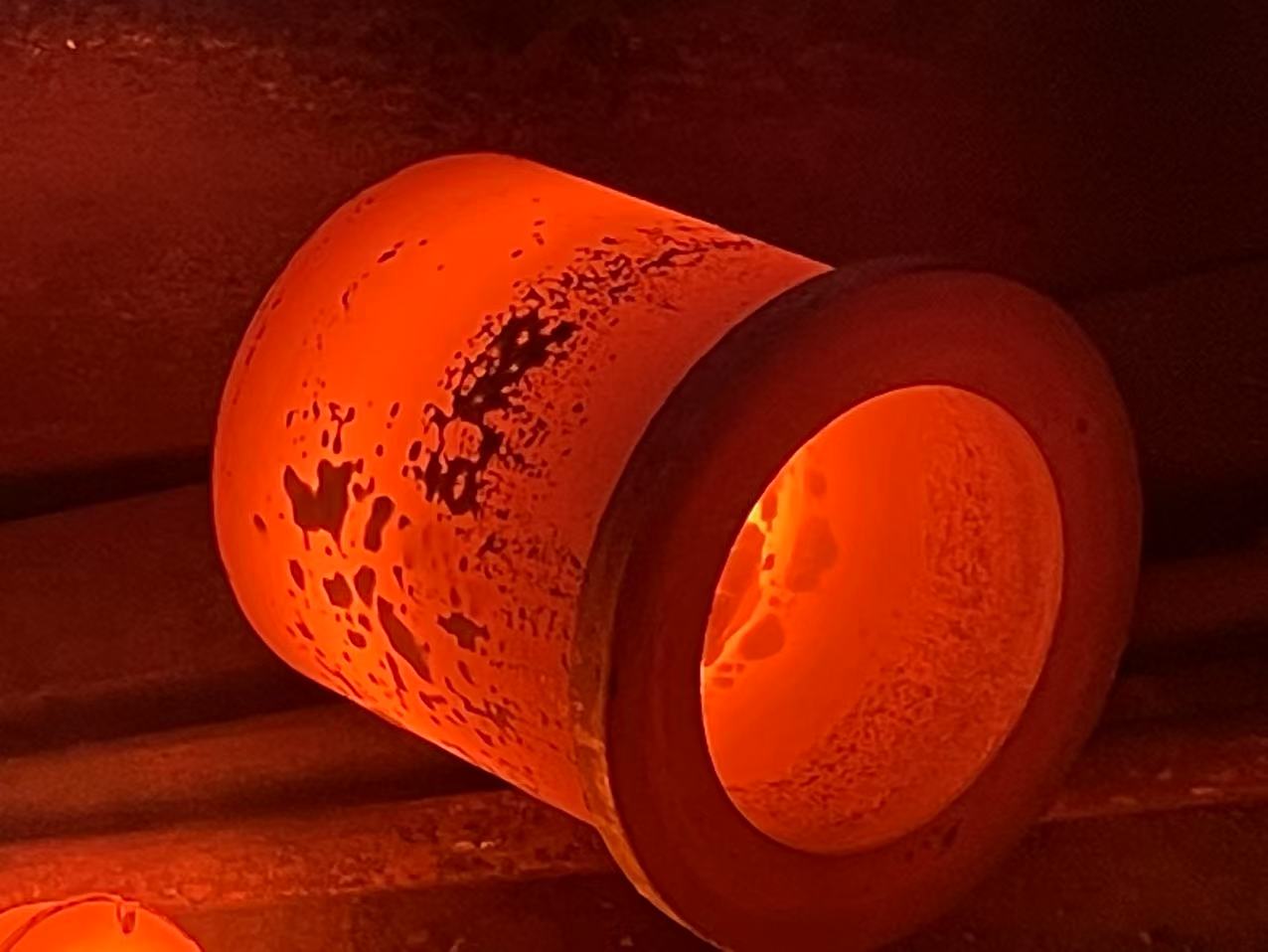
Forgiatura di ingranaggi grezzi (Hot & Ring Forging)
Produciamo sbozzi per ingranaggi ad alta resistenza:
- Fucinatura a caldo di ingranaggi grezzi con struttura dei grani migliorata e resistenza alla fatica
- Forgiatura ad anello per ingranaggi di grande diametro, per migliorare la concentricità e l’efficienza dei costi
- Prelavorazione di pezzi grezzi forgiati per consentire una minima asportazione di materiale
Materiali: Acciaio legato (42CrMo, 20CrMnTi, 18CrNiMo7-6), acciaio inossidabile, acciaio per utensili
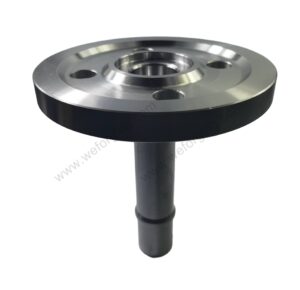
Processi di lavorazione degli ingranaggi
I nostri servizi di lavorazione degli ingranaggi CNC includono:
- Tornitura e fresatura CNC di ingranaggi grezzi forgiati
- Dentatura e sagomatura di ingranaggi per moduli da 1 a 12
- Taglio di scanalature, brocciatura e rettifica dei denti
- Finitura superficiale: cementazione, nitrurazione, tempra a induzione
Tutti gli ingranaggi sono lavorati secondo gli standard AGMA, DIN o ISO 1328, con un controllo preciso dell’errore di rotazione, della forma del dente e della deviazione del passo.
Panoramica delle attrezzature
Il nostro impianto di produzione di ingranaggi comprende:
- Dentatrici a controllo numerico (YKD315, YKD500)
- Macchine dentatrici e rettificatrici di profili
- Torni CNC verticali e orizzontali
- Centri di misura del dente e CMM
- Forni per il trattamento termico e laboratorio QC
Gestiamo lotti da 1 a 10.000 unità, con tracciabilità e ispezione per ogni pezzo.
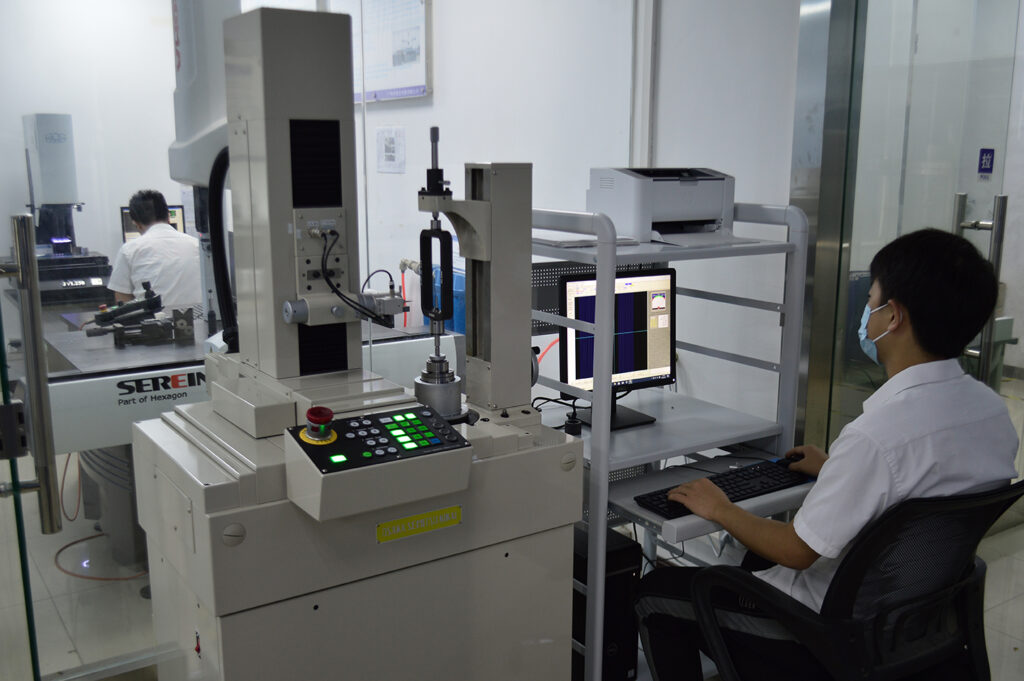
Applicazioni e settori
- Riduttori per macchine edili
- Ingranaggi di trasmissione per camion e macchine agricole
- Anelli dentati per turbine eoliche
- Ingranaggi di precisione per attuatori e azionamenti di valvole
- Ingranaggi per motori idraulici e componenti interni di pompe
Perché scegliere weforging per la lavorazione degli ingranaggi?
- Produttore di ingranaggi personalizzati con capacità di forgiatura e finitura completa
- Lavorazione CNC di ingranaggi grezzi forgiati a caldo e ad anello
- MOQ ridotto e prototipazione rapida con utensili interni
- Certificazione ISO 9001 & CE
- Esperienza di esportazione in oltre 20 paesi
Il nostro team di ingegneri supporta il DFM, la revisione delle tolleranze e l’integrazione dei disegni 2D/3D. Tutti i prodotti sono sottoposti a ispezione al 100%.