Precision Internal Gears for High-Performance Power Transmission Systems
Premium Quality Internal Ring Gears Engineered for Demanding Applications
Our precision internal gears are manufactured to deliver exceptional performance in planetary gear systems, gear reducers, and other critical power transmission applications. Utilizing high-grade materials and advanced machining processes, these gears ensure smooth operation, high torque capacity, and extended service life in the most demanding conditions.
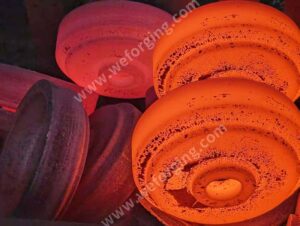
Key Features & Benefits
✔ Superior Material Selection
High-Strength Materials: SAE 4340, 4140 alloy steel or case-hardened steel
Advanced Heat Treatment: Carburizing/induction hardening for surface hardness up to HRC 60-62
Low-Friction Finishing: Special tooth surface treatment for improved efficiency
✔ Precision Engineering
CNC Gear Cutting: Compliant with AGMA Class 8-10 standards
Optimized Tooth Profile: Precision ground for smooth meshing & reduced noise
Strict Quality Control: 100% inspection of internal diameter and tooth geometry
✔ Enhanced Performance
High Torque Capacity: Up to 10,000 Nm
Quiet Operation: Optimized tooth profile minimizes vibration
Extended Durability: Hardened surfaces for longer service life
✔ Customization Options
Module Range: 1 to 12
Tailored Dimensions: Custom internal diameters and face widths
Protective Coatings: Phosphate, black oxide, or nickel plating
Industrial Applications
Planetary Gear Systems
Industrial Gear Reducers
Wind Turbine Gearboxes
Heavy Construction Equipment
Mining Machinery Transmissions
Competitive Advantages
✔ Quality Certified: ISO 9001:2015 compliant manufacturing
✔ Performance Guaranteed: Rigorous fatigue and durability testing
✔ Global Compliance: Meets AGMA, DIN, and ISO standards
✔ Fast Delivery: Standard configurations available from stock
Why Choose Our Internal Gears?
Precision-manufactured for optimal power transmission
Custom-engineered solutions for specialized applications
Proven reliability in extreme operating environments