What is the Difference Between Cold Forging and Hot Forging?
Introduction
In modern manufacturing, forging is one of the most reliable methods to produce strong, precise metal parts. But when choosing between cold forging and hot forging, many buyers wonder: what’s the real difference? Understanding this helps you select the right process for custom forged components, ensuring you get the best performance, cost, and quality.
In this article,Weforging Manufacturing will explain the key differences, applications, advantages, and typical industries using each process.
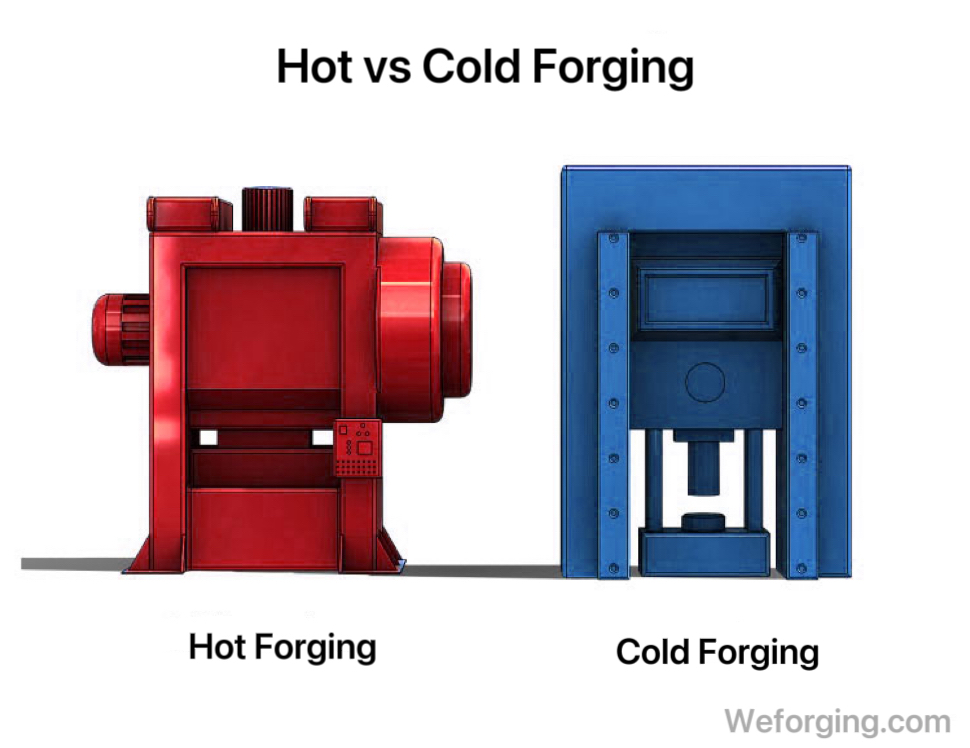
What is Cold Forging?
Cold forging, also known as cold forming, is a forging process done at or near room temperature. The metal is forced into a die under high pressure.
Cold forging is ideal for creating precision forged parts with excellent surface finish and tight tolerances.
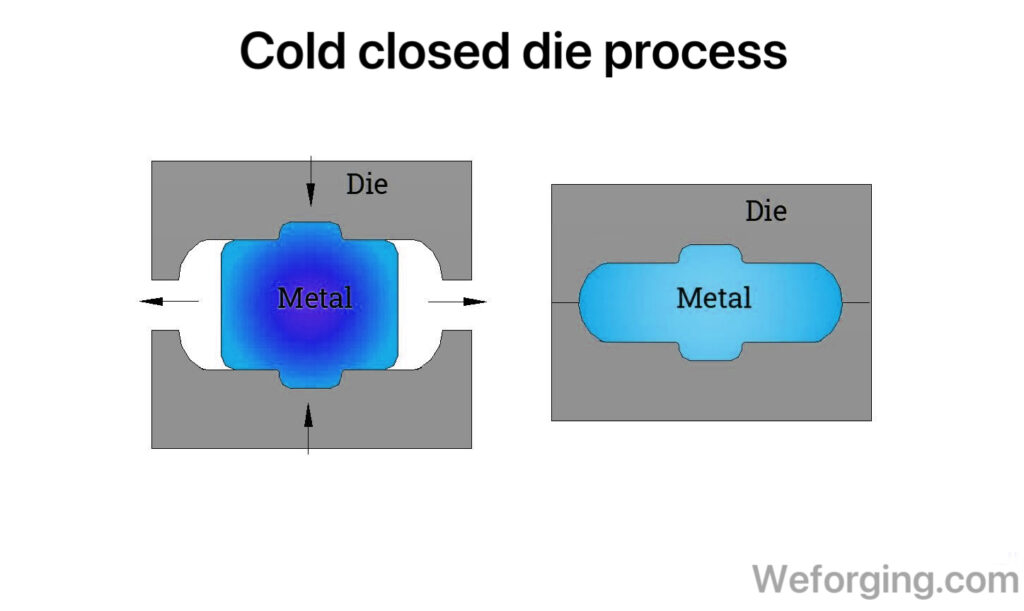
Main Features of Cold Forging
No heating required
→ Results in significantly lower energy costs.High dimensional accuracy
Forging precision can be controlled to about ±0.1 mm per side.
For unprocessed surfaces, this reduces subsequent machining costs.
Smooth surface finish
Free of oxide scale, improving surface quality and reducing secondary processing needs.
Material limitations
Suitable for relatively soft metals, such as 1045, 20#, and materials with low alloy content.
Smaller components
Cold extrusion capacity
Allows slightly larger parts (typically up to 1–2 kilograms), depending on material and shape:
splined shafts, sleeves, and retaining rings.
Batch quantity requirement
Due to the high cost of molds, cold forging is suitable for mass production only.
For example, cold-forged fasteners typically require 200,000+ pcs per batch to be cost-effective.
What is hot forging?
Hot forging refers to the deformation of metals above their recrystallization temperature, typically between 900°C and 1250°C for steel.
Heated metals are malleable, thus making it easier to shape large and complex components.
Main features:
It is applicable to various metal materials and high-strength alloys
- It has better formability for large parts
- Reduce internal stress and improve grain structure
- The forging impact force is large, so the reserved allowance of the product is relatively large. To improve the precision, additional processing may be required, and the consumables will be relatively large, but the versatility is stronger
- There is an oxide scale on the surface, and further surface treatments such as shot blasting are required
Typical hot forging products include ring forgings, gears, shafts, flanges, and heavy custom forgings for automobiles and heavy machinery.
Cold Forging vs. Hot Forging: Key Differences
Feature | Cold Forging | Hot Forging |
Temperature | Room temperature | 900–1250°C |
Material Hardness | Softer metals preferred | Works with tough alloys |
Accuracy | High precision | Good, may need machining |
Energy Use | Lower | Higher (heating required) |
Typical Parts | Fasteners, small precision components | Gears, ring forgings, shafts, heavy-duty parts |
If you need high-volume small parts like fasteners with precise tolerances, cold forging is the best choice.
If you require large, strong components such as custom forged gears or ring forgings, hot forging offers superior mechanical properties.
Benefits of Weforging Manufacturing’s Custom Forging
At Weforging Manufacturing, we offer custom forging solutions covering both cold forging and hot forging.
We control the entire process — from raw material selection, forging, CNC machining, heat treatment, to final inspection.
Our advanced facilities ensure tight quality standards, whether for precision fasteners, ring forgings, or complex gear forgings.
Watch How We Forge
Below is a short video from our Weforging YouTube channel showing a quick look at our forging lines:
Conclusion
Choosing between cold forging and hot forging depends on your product requirements — size, material, precision, and budget.
Partnering with an experienced supplier like Weforging Manufacturing helps you get high-quality, cost-effective forged parts that meet your exact specifications.
If you’d like to discuss your custom forging project, feel free to contact us today!
Email:wf-kevin@outlook.com
Web:www.weforging.com